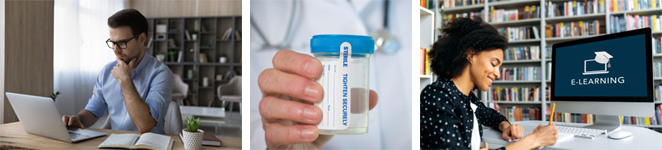
Drug Test/Screening Collector Training & Certification, Milton, NH
For
Collection Sites, Medical Facilities, DER's, HR Managers, Safety Managers, Court Personnel, Probation Officers, TPA's
Accredited Drug Testing provides a comprehensive online/web-based Urine Drug Testing Collector Training and Certification course in Milton, NH for persons required as part of their responsibilities to perform or supervise urine drug testing specimen collections. The collector training program may be completed with or without the required mock collection proficiency assessments. Upon completion of the training program, students will receive a certificate of successful completion of the training course. In Milton, NH to be qualified/certified as a DOT urine drug test collector, you must satisfactorily complete both the training course and a minimum of 5 error free proficiency mock demonstrations.
The Drug Test Collector plays a critical role in the workplace drug screening process. Along with the employer, the testing facility and the Medical Review Officer (MRO), the collector is an essential part of a system developed to ensure drug-free workplaces for the sake of public safety.
As the collector, you are the only individual in the drug-testing process who has direct, face-to-face contact with the employee. You ensure the integrity of the urine specimen and collection process and begin the chain of custody that includes the laboratory; the MRO; the employer; and, possibly, the courts.
This training is a professional-level course that provides the knowledge and skills to qualify Drug Test Collectors to perform U.S. Department of Transportation-regulated drug tests and non-regulated tests. Course participants also have the option of becoming professionally certified after completion of this course. This designation confirms that the collector is committed to the highest standards in the drug and alcohol testing industry.
The Course
This professional-level course meets the regulatory standards of U.S. Department of Transportation (DOT) rule 49 CFR Part 40 and provides a solid foundation for a wide range of testing programs.
- Library of terms & resources
- Universal skills set
- Multiple industries
- Lessons
- DOT Qualification
- Public sector
- Short quizzes & final examination
- Professional Certification
- Private sector
- Mock collections
- Regulated by local, state and federal authorities
- Signature
How to become a DOT Qualified Urine Collector?
To become qualified as a collector, you must be knowledgeable about Part 40 regulations, the current "DOT Urine Specimen Collection Procedures Guidelines," and DOT agency regulations applicable to the employers for whom you will perform collections, and you must keep current on any changes to these materials. You must also (1) successfully complete a qualification training program and (2) pass a monitored proficiency demonstration, as required by DOT regulations [See 49 CFR Part 40.33 (b-c), effective August 1, 2001]. Please note: there is no "grandfather" clause or waiver from this requirement. A collector's qualifications are not location/collection site specific, and their eligibility will follow them anywhere DOT Agency regulated urine specimens are collected. There is no requirement for qualified collectors to register or to be on any federally-maintained or federally-sponsored list, but they are required to maintain (for Federal inspection) documentation of successful completion of their training and proficiency demonstration requirements.
How to Take the Course
The Drug Test Collector Training involves multiple parts that need to be completed in a specific order to achieve certification.
- Before starting the training, the collector must:
- review 49 CFR Part 40 and be familiar with the regulatory language;
- review the DOT Urine Specimen Collection Guidelines;
- review "Instructions for Completing the Federal Drug Testing Custody and Control Form for Urine Specimen Collection"
- watch DOT's 10 Steps to Collection Site Security and Integrity video.
- and download the sample Custody and Control Form. This form guides the entire drug-collection process. Review the document and have it at hand through the entire course. (All required materials are also available in the Reference Library.) NOTE: The 2017 version of the CCF is no longer current. If you intend to use it, you must attach a Memorandum for Record (MFR).
- Take the course Pre-Test to show familiarity with the subject matter based on a review of the materials provided.
- Complete the lessons of the training along with the required short quizzes.
- Take the final exam. A score of at least 90 percent is required.
- When you pass the online portion of this training, continue to the Next Steps lesson for instructions on how to set up five mock collections with a live examiner. These must be scheduled within 30 days of course completion and are required for qualification and certification.
- Once the mock collections are completed without error, you will be qualified and can perform both federally regulated and non-regulated drug test collections.
- To be certified, qualified collectors are asked to sign an agreement promising to adhere to the standards set in the training. The course administrator will then issue a certification form documenting that the collector is both a USDOT Qualified and Professionally Certified Drug Testing Collector. Contact the course administrator for more information.
Additional Courses Available
- DOT Alcohol Screening Test Technician Training
- Saliva/Oral Fluid Training & Certification
- Certified Drug Test Collector Annual Exam
- DOT Breath Alcohol Technician Training
- Hair Specimen Collector Training & Certification
- DOT Reasonable Suspicion Training Course
- DER Training FMCSA
- DER Training FAA
- DER Training PHMSA
- DER Training FRA
- DER Training FTA
- DER Training USCG
- MRO Assistant Training
- New Business Start Up Overview
** Accredited Drug Testing's Urine Specimen Collector training course is developed in conjunction with the National Drug and Alcohol Screening Association.
Drug and Alcohol Testing Locations Milton, NH
40 WINTER ST STE 200 6.7 miles
ROCHESTER, NH 3867
11 WHITEHALL RD 7.1 miles
ROCHESTER, NH 3867
21 CLARK WAY 11.3 miles
SOMERSWORTH, NH 3878
13 JULY ST 11.8 miles
SANFORD, ME 4073
396 HIGH ST 12.4 miles
SOMERSWORTH, NH 3878
750 CENTRAL AVE STE E 14.3 miles
DOVER, NH 3820
545 MAIN ST 18.0 miles
WATERBORO, ME 4087
114 Sanford Rd 21.0 miles
Wells, ME 4090
20 DAME RD 21.9 miles
NEWMARKET, NH 3857
25 New Hampshire Ave Ste 105 23.6 miles
PORTSMOUTH, NH 3801
Were you looking, instead, for:
All Rights Reserved
Milton is a town in Strafford County, New Hampshire, United States. The population was 4,598 at the 2010 census. A manufacturing, resort and residential town, Milton includes the village of Milton Mills. The primary village in town, where 575 people resided at the 2010 census, is defined as the Milton census-designated place (CDP), and is located along New Hampshire Route 125 and the Salmon Falls River, just north of Route 75.
Originally a part of Rochester variously called the "Northeast Parish", "Three Ponds" or "Milton Mills", the town was settled in 1760. It was set off and incorporated in 1802 as "Milton", the name either a contraction of "mill town", or else derived from a relative of the Wentworth colonial governors — William Fitzwilliam, Earl Fitzwilliam and Viscount Milton. The town of Fitzwilliam also bears his name.
The high concentration of water powered industries in Milton caused Ira W. Jones to found and operate an engineering firm from offices on Main Street in Milton. The company did business as I W Jones Engineers.
In 1893 Jonas Spaulding opened a leatherboard mill in Milton, organizing the business as J. Spaulding and Sons. His sons were Leon C., Huntley N. and Rolland H., of whom Huntley and Rolland would serve as governors of New Hampshire. Jonas and his sons would undertake the construction of another leatherboard mill in North Rochester around 1900. Jonas died before the North Rochester mill became operational. The brothers continued to run the business successfully and brought the Spaulding Brothers leatherboard mill in Townsend Harbor, Massachusetts, under the J. Spaulding and Sons banner in 1902. They were successful with a machine to manufacture shoe counters and with experiments to make vulcanized fibre. In 1912 they opened a purpose-built facility to make vulcanized fibre in Tonawanda, New York. In 1913 J. Spaulding and Sons opened a second leatherboard mill in Milton. They also acquired the Kennebunk Manufacturing Company (KEMACO), which made lunch boxes and violin cases using leatherboard and vulcanized fibre and at one time had facilities in Milton as well.